Furnace Description
The superb insulation allows for excellent melting
performance from the high performance compact gas burner.
Radiation losses are minimised by use of a well-insulated
swing-aside cover that can be sealed when no baling
or filling is needed. A low casing temperature provides
comfortable working conditions
RADIANT PANEL ASSEMBLIES
Twelve refractory, radiant heater panels are arranged around
the crucible and extend to the full depth of the furnace chamber. The self-supporting design facilitates ease of removal in the unlikely event the panels need replacement. These panels
efficiently convert gas energy to radiant energy.
HIGH EFFICIENCY
The combination of radiant heat transfer and the use of
advanced insulating materials provides a melting and holding
furnace of exceptional efficiency and comfortable working
conditions.
SIZE RANGE
The furnace is available in sizes ranging up to 1327 kg for
melting. Other crucible patterns than those shown in the
performance table are available to provide the capacity span
indicated for each size reference.
FUELTYPES
Natural Gas: 9000 Kcal/m
3
Propane: 22000 Kcal/m
3
Butane: 28000 Kcal/m
3
Pressure: 20—millibar
PERFORMANCE DATA
*Data for zinc and zinc alloys available one request.
Above data based on optimum foundry conditions. For normal foundry operations a performance of 90% of these ratings is typical.
KEY FEATURES :-
GAS BURNER
The furnace is equipped with an advanced self-contained nozzle
mix gas burner. The burner provides maximum melt rates with
efficient fuel inputs. This maximises crucible life and
performance. The controller and fast response rate of the
furnace nearly eliminate temperature overshoot.
This reliable, fully-modulating industrial grade burner utilises
anultra-violet detector to monitor the presence of combustion.
Accurate ratio control minimises emissions of NOx and CO.
CONTROL PANEL
- Circuit breaker for isolation and protection
- Proportional control gas burner
- Crucible and heater hour meters
- Programmable time clock switching
- Mimic display
- Flame failure, sequencing controller
Metal temperature control may be either from a floating or
fixed pyrometer or one housed within the crucible.
The programmable controller will maintain the metal
temperature within very close limits, by automatic adjustment
to heat input, whether melting or holding.
The digital display shows both the required temperature and
current metal temperature.
TEMPERATURE DEPRESSION
This energy conservation feature enables a lower holding temperature to be automatically selected during periods of non use. A dedicated real-time/date clock can be programmed to select reduced temperature and to return to operational temperature. when required. Similarly, the real-time clock can be programmed to start up and shut down the furnace at preset times and dates.
OUTPUT LIMITED
THERMOCOUPLE FAILURE PROTECTION
If the thermocouple sensor fails, this feature provides a programmed level of output power. Typically set to 10-30%, the time proportioning power control provides sufficient heat output power to maintain an aluminium charge within an acceptable temperature range.
lifespan.
POLICEMAN CONTROL
The furnace is equipped with a ”policeman” control. This feature is designed to prevent overheating of the furnace refractories and radiant panels, thus avoiding reduction of their lifespan.
PYROMETRY
A variety of metal temperature pyrometry can be specified. This Includes floating or fixed immersion types and thermocouples housed within the crucible for holding applications.
OPTIONS AVAILABLE
Spilt metal detection, low metal temperature alarm, in-range indicating beacons, pneumatic swing-aside cover, and metal temperature overshoot control
SPECIFICATIONS NOTE: Opposite hand available. *increased furnace height.
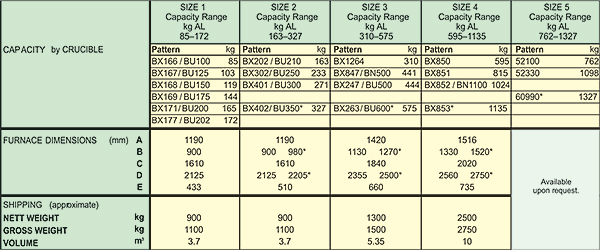